Monkeypod Bookmatched Dining Table
Note: I drafted this blog in the beginning of December, 2019. I got through most of the writing, but I hadn’t finished editing the photos and videos showing the build process. So, now you’ll be reading this blog almost at the end of 2020. I love working on these blogs, but taking care of my current clients always takes priority. Somehow, I’m finding time on a Sunday afternoon to wrap this one up. Instead of the Lagavulin right now, I’m drinking iced sparking water.
2019 has been quite the year. I’m sitting here at the computer with a glass of Lagavulin 16, a great scotch that was just for sale at Costco for $42 — $10 off of its normal price. I was too frugal to buy two bottles, but since its one of my favorite whiskies I’ll inevitably buy another bottle for the full price in a couple months. [Update from 8/2020: Lagavulin 16 is now $68 at Costco. Too expensive for a furniture maker.] If that, or any of the following, doesn’t make sense, we can blame a half glass of extremely reasonably priced whisky.
My goal for this year was to build a large commercial piece — I was thinking of a buffet table for a hotel, maybe some retail store fixtures, or a bar top. I got outbid for most of those jobs that came my way, but one came through — pieces for a restaurant. Working on a restaurant ended up being the most challenging project of my career in many ways, but that is not what this blog post is about. This blog post is about another goal I fulfilled — building a Nakashima Conoid style dining table.
George Nakashima was an American woodworker of Japanese descent, and he popularized a style of furniture that I find extremely aesthetically pleasing. I won’t go too much into Nakashima, but his book Soul of a Tree is well worth reading to learn about his journey and philosophies. Nakashima’s style of furniture was centered around the slab, taking care to build furniture that preserved the wood’s natural character. I don’t think we can say that Nakashima invented the slab table, but he certainly helped popularize it.
Nowadays, slab tables are common. Monkeypod slabs from Indonesia can be found at Home Depot. There are tons of local and imported slab tables that are virtually indistinguishable from one other. Just a finished slab with some sort of legs attached. Most of them look like junk, and in a few years they will barely be worth the wood that they’re made from. It also doesn’t take an expert woodworker to make a basic slab table. It feels weird to call myself an expert woodworker but lets just use the 10,000 hours definition. One can make a slab table with a circular saw and a belt sander (literally thats all you need… I’m not kidding). Military guys who were stationed on Oahu since the 1960’s have been building slab tables in their free time and sending them home as a token of their time spent on island. I’ve seen some of them, and they look great!
None of this is meant to denigrate the concept of a slab table. My point is only that they’re not special, which is why I generally don’t like making them. Here’s my thoughts.
The price issue. My time is fairly valuable (not lawyer-valuable), but I have to charge at least $5,000 to make a monkeypod slab table. I could teach a kid to sand a slab and make a base (which is incidentally how I got into woodworking… I was that kid), in just about a weekend. A handy lady or man could spend a few weekends getting dusty with a sander and make themselves a slab table, and save their $5,000. Well, maybe $3,500… they still have to buy the slab and a whole lot of sand paper. $3,500 is a lot of coin in Hawaii, so for most people its just not going to be worth it for them to buy a basic slab table from me.
There are very few design elements that go into a basic slab table. What are our options with a slab? Cut the ends straight? As a woodworker, a large part of my enjoyment is in the design process. The concept of a slab table takes that away. Even trying to design a completely minimalist table is more exciting than a slab table — at least the former has room to become more and more refined.
This is kind of a continuation of #2, but the market for slab tables is oversaturated. There are so many slabs being imported from Asia, in both finished and unfinished form. While having a slab table made by me is going to be much better quality than an imported table, the end product will look much the same.
All that said, having a slab of wood in your home is a magical feeling. In our modern world, so filled with technology, metal, concrete and plastic, an organic piece of wood brings a very welcome and comforting sense into the home. So, the question becomes how to introduce a natural statement into your home without being boring and cliched. In my opinion, its all about the base.
The base is where Nakashima excelled. It’s just as strong and stable as it needs to be, no more, no less. If you remove one element of the base, the design ceases to function. The proportions are perfect, the lines are clean, and the design seems to proudly accent the organic slab top. Above is a table base built by me, but its as close of a copy to Nakashima’s original design as I could manage. I wish I had a copy of Nakashima’s table to study in person, but they regularly sell at auction for $50,000-$100,000, so studying one is a little out of my price range.
Nakashima’s designs are also elegant in that they don’t use any fancy technology, CNC machines, or screws. The base could be built using only a chisel and saws. I used plenty of power tools for speed and precision, but the joinery is similar to what Nakashima used. Lets look into it!
These bridle joints are rough cut on the table saw, and then cleaned up with chisels.
You can see a bulk of the joinery is already cut out in this picture.
Glued up the first part of this monkeypod base.
When finishing, the inside of the joints are taped off to allow glue adhesion when the pieces are put together. I get cleaner results by finishing the pieces separately and gluing the joinery after.
Now that the feet of the base are done, we turn our attention to the vertical elements. These pieces form the core structure of the table — they have to support the entire weight of the slab. So, I used laminated solid monkeypod for extra strength, stability and thickness. This process also allowed the two legs to be perfectly matching. If you look carefully at the legs, you’ll see that each vertical piece is made of 1” thick pieces of solid monkeypod, glued together.
The pattern routing process leads to the legs below, and now the base can be put together for the first time!
At this point, the base is ready for glue! The dry fit is important part of the joinery process, and there is a lot of fine tuning during the dry fit to ensure that the parts fit together perfectly. Once the fit is perfect, we can add glue!
Now the base is pretty much done. I’m going to share a quick gallery of gluing up the top, although putting the top together is not nearly as interesting as building this base.
Then, as the last part of this table’s journey, it got crated up and shipped (well, flown) to the mainland U.S. Goodbye!
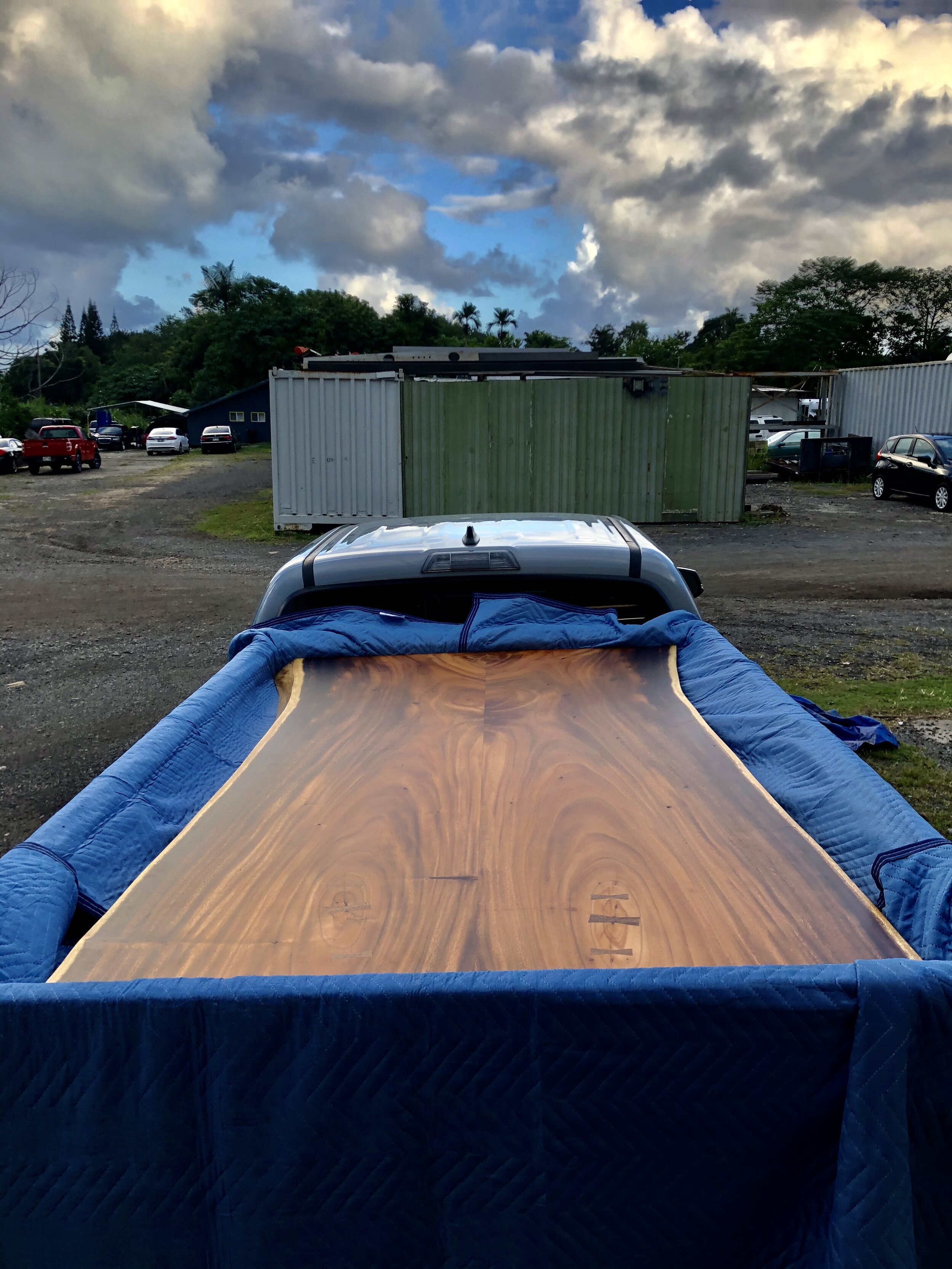
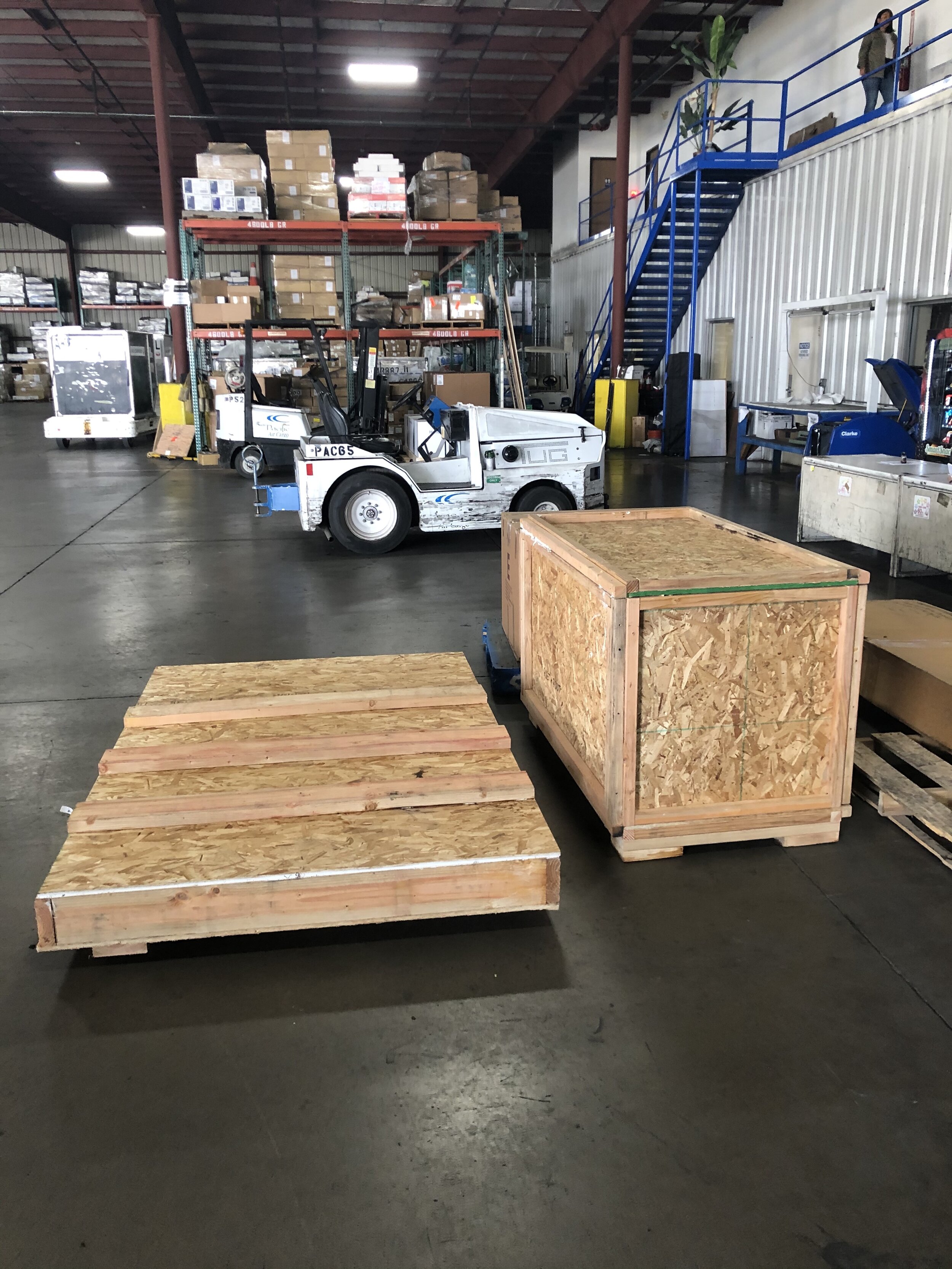